
Housing covers have additional benefits, as well. This is easily correctable by installing an ejector housing cover or shield. That can cause the ejector plates to try to bend the next time the mold cycles. It is not that uncommon for small molded parts with undercuts on their cores to ricochet off the cavity upon ejection and end up inside the ejector housing. If the machine’s retract position is not set properly, ejector bars can pull and distort a poorly supported ejector plate.Įjector housings are typically open on two opposing ends of a mold, and one of the open ends is often at the top when mounted in the machine. Having rest buttons near the tapped holes for the machine’s ejector bars is also beneficial. It is a good idea to have a rest button near or under any component that could apply pressure to the ejector plate, such as a lifter or an ejector pin that butts up against steel. This is when you can get a support problem. On occasion, rest buttons are moved or eliminated to make room for a core pin or some other component. The purpose of these rest buttons is to minimize the contact area between the two plates, to allow some debris to accumulate without affecting the proper position of the ejector system. If any ejector pins are under a cam, the pin or the cam can get damaged when the mold closes. Protruding pins can cause sticking issues when trying to eject the part. Those designs are notorious for bending or breaking the retainer plate.ĭid you ever wonder why molds have those round stop pins or rest buttons between the ejector plate and the clamp plate? They are there because if any dirt or debris gets in between these two plates, some or all the ejector pins are going to protrude beyond the parting line of the mold by an amount equal to the thickness of the debris. If you have your own design, make sure the extensions do not butt up against the back of the ejector retainer plate. Several mold-components suppliers sell standardized knock-out extensions. If the mold has knock-out extensions attached to the ejector plate, and they are not the same length, or one of their retaining bolts comes loose, this too can cause an uneven load on the ejector plate. Bars that are too long or of different lengths are the primary reason for bent ejector crosses. If you have an ejector-plate deflection issue, the root cause of the problem is probably not the thickness of the plate.Ī more common condition that will apply an uneven load to the ejector plate is if the molding machine’s knock-out bars are slightly different lengths. Steel crosses that are bent can be straightened out in a hydraulic press, but cast-iron crosses will probably crack.
The demolding force required for complex structures is large, and the number of ejectors should be increased accordingly.This condition is usually obvious because the machine’s knock-out bars may not align with, or will rub against, some of the through holes in the moving platen.

(1) The ejector pins should be arranged so that the ejection force is as balanced as possible. They let technicians apply a force to eject a part from the mold, and, in some cases, can leave marks. Ejector pins are the “bouncers” of the injection molding world.
EJECTOR PIN MARKS HOW TO
Here are some tips on how to properly locate and use those pins. They have terrific heat-transfer properties and are very resistant to galling.Įjector pins help safely remove parts from molds after they have been made. While many molders use core pins made of copper alloys, there are many benefits of using them for ejector pins as well. Once the mold is opened, the pins extend into the mold cavity, push the part out, and then retract, allowing the mold to close and be refilled.

They apply a force to eject a part from the mold, and in some cases can leave marks.
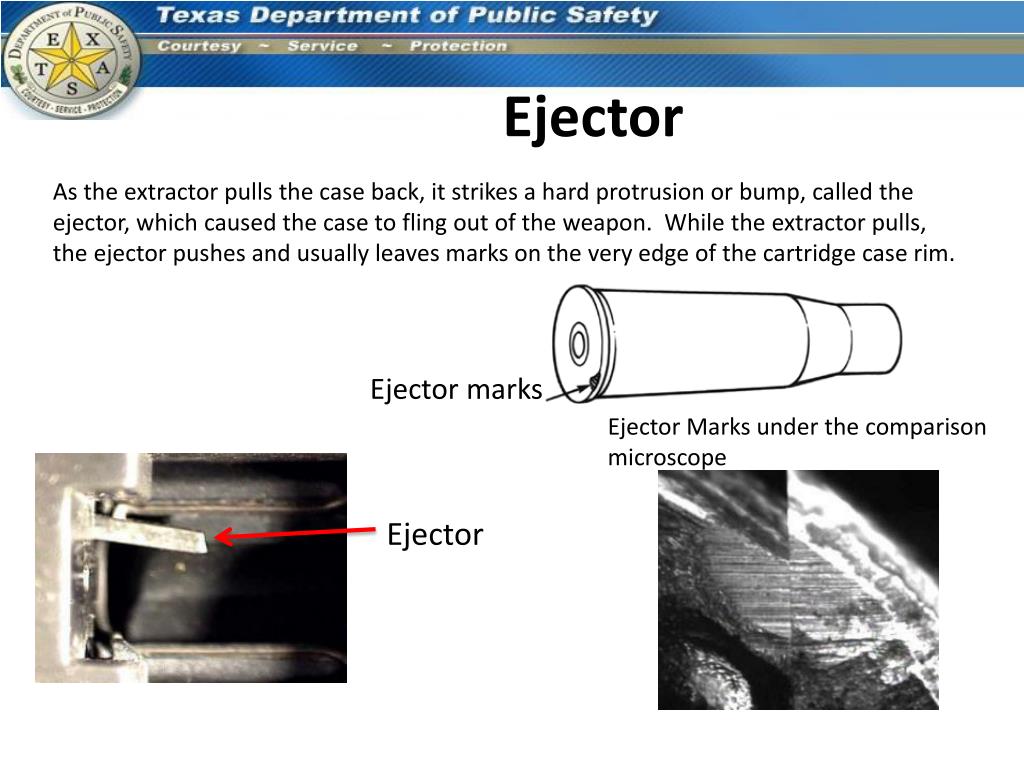
Ejector pins are the "bouncers" of the injection molding world.
